Hilton Foods and the power of the MES system
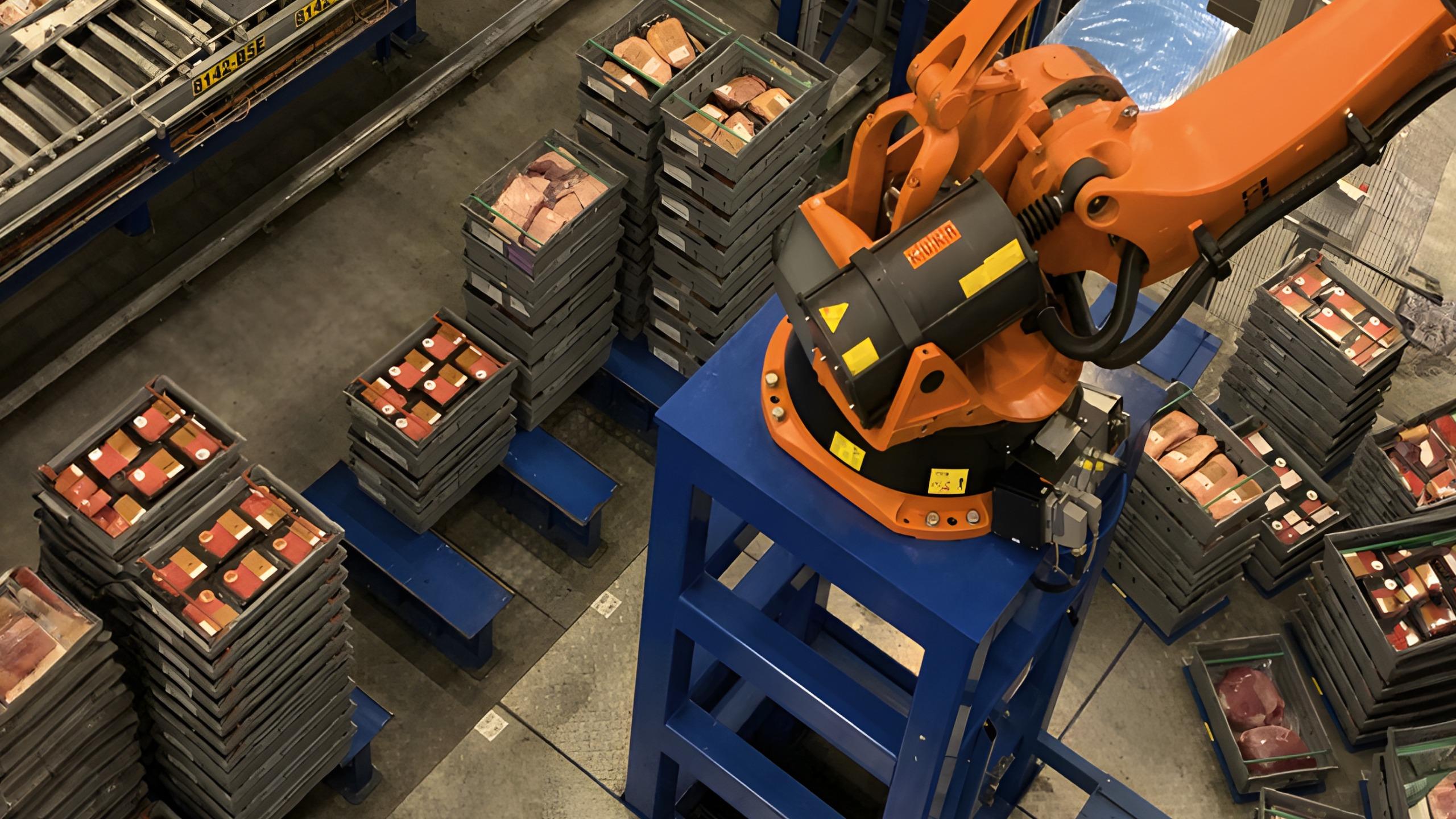
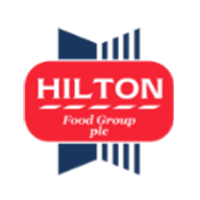
Hilton Foods took on the challenge of improving its production process by introducing automation and reducing human error. Through a customized Manufacturing Execution System (MES) developed by Euvic's team, Hilton Foods was able to streamline the management of over 200 production lines.
Client:
Hilton Foods
Industry:
Manufacturing
Country:
England
Services:
MES-system
Summary
Hilton Foods embarked on the task of enhancing its production workflow by implementing automation and reducing human error. Utilising a tailored Manufacturing Execution System (MES) crafted by Euvic’s experts, Hilton Foods successfully optimised the oversight of more than 200 production lines
Intro
Established in 1994 as a central meat packing facility in Huntingdon, England, Hilton Foods has expanded significantly, now operating six factories across Europe along with two joint ventures. Their products are distributed across 14 European countries, Australia, and New Zealand.
Challenge
Hilton Foods encountered several challenges, each with clearly defined goals:
- Automating production processes to maintain continuous control over execution.
- Minimising the risk of human error by standardising processes and reducing manual input of production data.
- Implementing a system for monitoring production performance and quality, including key performance indicators and built-in reports.
- Transitioning to a paperless organisation, aiming to reduce paper forms and reports to streamline operations.
Solution
To address Hilton Foods’ challenges, Euvic’s team devised a bespoke solution, introducing a Manufacturing Execution System (MES) to optimise production execution and control. This system, tailored to accommodate Hilton Foods’ complex and high-volume production environment, showcased impressive capabilities:
- Scalability to support over 200 production lines, with the ability to handle up to 120 trays of meat per minute per line.
- Integration of over 1,000 devices for real-time monitoring and control of production processes, effectively reducing human error and ensuring data integrity.
- Implementation of RFID technology for automated tracking, enhancing traceability and product handling.
Result
The implementation of the MES system yielded significant results for Hilton Foods:
Production data collection: Efficient collection of detailed production data, enhancing overview and control of processes.
Data exchange with external systems: Seamless data exchange with external systems such as ERP and WMS, ensuring integrated operations.
Product specification generation: Automated generation of product specifications, contributing to consistency and accuracy of information.
RFID package programming: Streamlined traceability and handling of products through RFID package programming.
Downtime management: Effective downtime management, minimising disruptions and increasing productivity.
Calculation of key performance indicators: Precise calculation of key performance indicators for continuous monitoring and evaluation.
Reporting system: Provision of comprehensive reports for operators, team leaders, and management, facilitating informed decision-making based on real-time data and analysis.